Chemicals For Continuous Galvanizing Line
Chemicals For Continuous Galvanizing Line
MAJOR STEPS FOR CGL
Galvanizing is a process of imparting a sacrificial zinc coating on the iron or steel surface, thereby protecting the surface from atmosphere. Method of application differs according to the need and availability of measures.
The most popular galvanizing method is Hot Dip Galvanizing which is adaptable to almost all types of fabricated and non-fabricated items. Flux type Continuous Galvanizing Line is such a kind where iron or steel strips are degreased, pickled and fluxed for surface preparation before dipping into the molten zinc.
MAJOR STEPS:
ALKALINE CLEANING – Removing oil, grease and soil from steel surface is crucial, otherwise dissolution of iron oxide / scale by pickling will be retarded.
ACID PICKLING – Ferrous metals have a surface coating of metallic oxide and / or scale which must be removed before zinc coating can be applied successfully. Pickling involves immersing the work in an acid to dissolve the scale or oxide film.
FLUXING – Liquid flux is recommended for continuous galvanizing line (C.G.L). It is used directly without any dilution. It has the ability to keep the sheets free from oxides by removing the rust blush prior to dip in the zinc bath. It also improves the zinc – iron adhesion in the galvanizing process.
PASSIVATION – Chromate conversion coating chemical is applied on galvanized iron and zinc –aluminum surfaces. It imparts excellent corrosion resistive coating that protects the underlying surface from weathering.
In case of nonox lines no fluxing is required. Further, depending on the sheet condition, acid pickling stage may also be omitted.
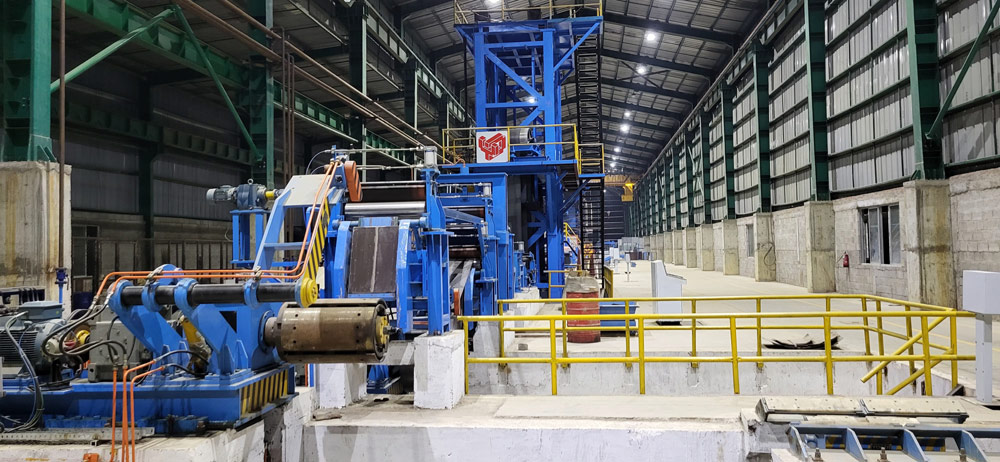