Liquid Nitriding And Oxinating Salt (QPQ PROCESS)
Liquid Nitriding And Oxinating Salt (QPQ PROCESS)
INTRODUCTION
Liquid Nitriding process involves enrichment of the Steel Surface basically with Nitrogen and very small amount of Carbon at a specified temperature range, by diffusion from Cyanide-free molten salt bath.
This thermo-chemical Transformation of the Steel surface enhances wear resistance, fatigue strength and anti-galling properties with least distortion and improves corrosion resistance.
It works very effectively for surface property enhancements on titanium, aluminum and chromium bearing steels as well as low alloy steels and stainless steels.
ENHANCEMENT OF PROPERTIES
Liquid nitriding increases wear resistance properties from 200% to 1000%, depending upon composition of base metal and fatigue strength by 20% to 100%.
PROCESS AND TECHNICAL DETAILS
Salt Bath Nitriding is performed at 560° – 570° C following necessary heat-treatment for core properties and finish machining. It ensures dimensional stability of processed parts and core properties which remain unchanged, provided heat treatment temperatures were higher than the liquid nitriding temperature, i.e. 560° – 570° C.
In liquid nitriding bath, which contains nitrogenous salts, nitrogen is released in a controlled and uniform manner at the interface of the work piece. Nitrogen by diffusion chemically combines with nitride –forming elements like aluminium, chromium and forms a tough ductile compound layer with high mechanical and chemical properties like hardness, wear resistance, anti-galling and resistance to corrosion.
Just adjacent and below the compound layer, another layer diffusion zone is formed. Diffusion zone consists of a solid solution of nitrogen in the base material. The diffusion zone contributes to substantial enhancement of fatigue strength. There is a simultaneous diffusion of carbon in a small amount which contributes to property enhancement combining with the base metal.
ADVANTAGES:
i) Liquid nitriding process is highly active, more efficient and time – saving compared to gas nitriding.
ii) After liquid salt bath nitriding the parts can be quenched in water, oil or cooled in air.
iii) The salt mixture is cyanide-free. So, the waste / carry over does not require treatment/ neutralization of toxic effect.
iv) The nitride parts can be given a bright lustrous black finish by a supplementary operation.
v) The thermo-chemical transformation involves negligible dimension change / distortion.
APPLICATION:
Liquid nitriding has unique advantages – improvement of surface properties like wear resistance, anti-galling and chemical property as corrosion- resistance. Process time & energy cost being low, the process is cost saving. It is non-hazardous being cyanide-free.
Considering these, the process has wide application in automobile and other industries. The process is widely used for surface hardening of gears, cam shaft, spindles , slides and guides engine valves, bushes , flanges , aluminium Extrusion dies, hydraulic components, high speed steel tools, mining machineries, husking machines, pump bodies and many others.
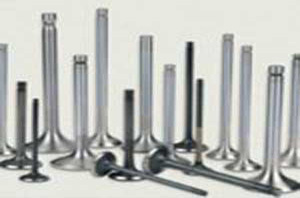
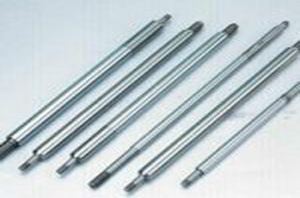
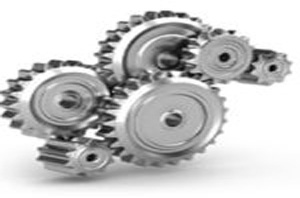
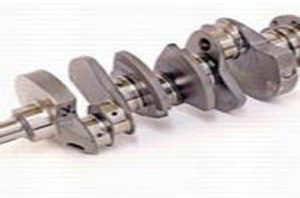